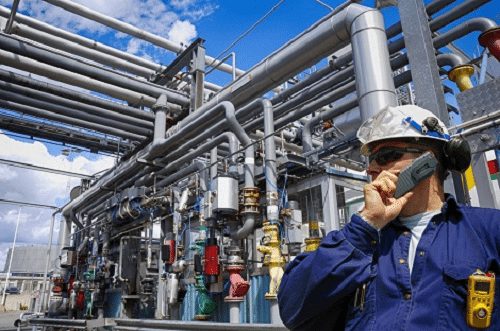
It only takes one small piece of equipment within an oil or gas pipeline to fail to cause an environmental disaster or endanger workers’ lives. The extensive list of safety and efficiency issues involved in natural gas and crude oil pipelines continuously highlights the need for traceability of the materials used in and work performed on these structures.
What Traceability Entails
The beginning of tracking materials and work performed on the pipeline can be traced back to the early 1990s. But now, more companies are improving their traceability technology. They’re building software platforms to store, organize and generate information, even providing handheld devices for operators and construction managers to remotely connect to the program and have real-time information at their fingertips.
A comprehensive traceability program includes information on materials, work process, IT systems, organization and metrics, according to PricewaterhouseCoopers LLP. It links all the records for an entire pipeline, which connects every part of the supply chain of the construction and maintenance of a pipeline, increasing transparency.
Traditionally, traceability includes information on each pipe segment, pipe joints, valves and manufactured bends. Detailed information is stored, such as the manufacturer of a part, the facility of origin, date and time the part was manufactured, the source of the steel and any noted defects.
The data goes even deeper, though. Take a weld, for example. The software will have the number of the weld, its specific GPS location, the date it was performed, the name of who performed it, the type, weld procedure specification, the installation contractor, the weld qualification report, the name of the non-destructive examination contractor who tested it, the results of NDE and if the weld was ever repaired or cut out.
Why It Matters
The in-depth information gathered through a traceability initiative is critical to avoid production and safety issues. For instance, in a recent project involving Project Consulting Services, Inc., a mill identified an issue with a specific coil of steel, Richard Nemec wrote in Pipeline and Gas Journal. Because PCS used a traceability program, it was able to quickly identify the joints made with that type of coil, repair the issue and avert disaster.
Traceability programs are important in the testing of the pipeline. Historically, field operators had little information on the materials and construction or repair process of the pipeline, but now, the electronically gathered and stored information is available to them. The program also stores data generated by the testing, which is crucial to documenting the system and planning for future construction.